IoT industriale (IIOT) al tempo del Covid-19: una leva preziosa per il futuro
Scenario
La pandemia ha causato una crisi dell’economia globale senza precedenti. I vari settori industriali a causa degli shock del mercato, sia in termini di offerta sia di domanda, sono stati costretti a ridurre significativamente i volumi di produzione con conseguente interruzione di intere catene di approvvigionamento. Laddove le imprese hanno continuato a produrre, le misure di distanziamento per il contenimento della pandemia stanno cambiando drasticamente gli ambienti di lavoro, le responsabilità dei dipendenti e la turnazione del personale.
Per superare l’attuale crisi e riprendere i livelli di produzione dopo il lockdown, le aziende devono essere in grado di: garantire la continuità aziendale; raggiungere un grado di resilienza tale da aumentare la propria “flessibilità” rispetto a uno scenario erratico; migliorare la propria performance a fronte di un mercato trasformato dalla pandemia e ritornare a operare con efficienza e competitività.
I dispositivi dell’IoT Industriale (IIoT) sono un elemento importante dell’Industria 4.0 e possono aiutare le aziende a perseguire questi obiettivi, come già dimostrato in molte occasioni negli ultimi anni; inoltre, la loro implementazione è destinata a diffondersi ulteriormente, a fronte del processo spinto di digitalizzazione in atto, supportato dal Governo, che si è assunto la responsabilità di promuovere incentivi e incoraggiare le aziende ad adottare tecnologie maggiormente abilitanti in più fasi della catena del valore.
L’impiego dei dispositivi IIoT per la continuità industriale
La buzzword del momento è garantire la continuità operativa. L’implementazione di dispositivi IIoT può essere determinante per garantire oltre alla continuità aziendale – anche nel ridurre al minimo il peso economico da sostenere in termini di safety & security del personale – migliorare la produzione e di conseguenza la liquidità, oltre a contenrere i costi di breve termine.
Di fatto, i dispositivi IIoT possono rivelarsi validi strumenti in termini di:
– operazioni da remoto per la riduzione del personale in loco, grazie alla manutenzione preventiva, nonché al costante monitoraggio dei livelli di produzione;
– monitoraggio della forza lavoro per far rispettare misure di distanziamento fisico essenziali indossando dispositivi di posizionamento che rilevano gli spostamenti all’interno di una struttura. Le informazioni, raccolte dai dispositivi IIoT, vengono elaborate da algoritmi intelligenti che aiutano a ottimizzare i flussi di lavoro, a ridurre al minimo il contatto ai cambi di turno ed evitare concentrazione di personale in alcune zone senza interrompere le attività. Inoltre, grazie all’installazione di Digital Heat Maps, è possibile rilevare la temperatura corporea del personale e, qualora qualcuno risultasse positivo al rilevamento, tramite dati di posizionamento dei dispositivi indossabili, sarebbe possibile informare i colleghi con i quali si è entrati in contatto. Naturalmente, tutte le informazioni specifiche del lavoratore devono essere rese anonime per proteggerne la privacy. Inoltre, se il Covid-19 costringesse parte del personale ad assentarsi a causa del contagio, i dispositivi sarebbero in grado di indentificare le aree operative impattate dall’assenza del personale dedicato, di notificare la situazione tempestivamente, intervenendo sulla programmazione della turnazione di lavoro con figure di back-up.
Considerando l’impatto del Covid-19 sulla supply chain e l’asincronia della domanda/offerta contingente, l’IIoT può rivelarsi un valido supporto in termini di:
- gestione dell’inventario – È possibile, grazie ai sensori dei dispositivi IIoT, monitorare i livelli di magazzino di ogni singolo sito o i materiali/materie prime lungo la filiera di approvvigionamento utilizzando i tag geografici in combinazione con la comunicazione mobile integrata, consentendo, in tempo reale, di gestirne il flusso in modo più accurato e di programmare gli ordini in modo tale da ottimizzare il magazzino;
- riduzione dei rifiuti – Il monitoraggio dei rifiuti, creati durante la produzione, permette di ovviare agli scarti e di ottimizzare la produzione, utilizzando meno materia prima e ottenere, così, una riduzione degli sprechi di materiale e una riduzione dei costi;
- monitoraggio delle materie prime – Gli approvvigionamenti delle materie prime vengono garantiti utilizzando informazioni in tempo reale sui livelli di magazzino e sulla capacità di produzione per determinare quali quantità devono essere ordinate e favorire rapide rinegoziazioni dei contratti. Questa caratteristica è particolarmente rilevante soprattutto in questo periodo di crisi, dato che ci si trova dinanzi ad una diminuzione dei prezzi di materie prime e la relativa rinegoziazione può produrre risparmi sui costi di produzione e garantire maggiori margini (es. il petrolio e il rame registrano una diminuzione del prezzo pari al 20-25%);
- cicli di manutenzione più lunghi – L’ottimizzazione dell’utilizzo dei macchinari e il monitoraggio dello stato di usura delle singole parti, favorisce la manutenzione preventiva e può generare un risparmio dei costi di manutenzione sino ad un 10-15%;
- ottimizzazione degli asset – I sensori permettono di effettuare delle analisi avanzate per aumentare l’efficienza di produzione di macchine singole o intere linee di produzione, ottimizzando i parametri di processo. L’algoritmo, di fatto, analizza le informazioni su tutte le variabili disponibili in termini di produzione, programmazione e monitoraggio della condizione dell’asset. Pertanto, le aziende possono avvalersi dell’IIoT per apportare importanti miglioramenti all’OEE (Overall Equipment Effectiveness, i.e. efficienza delle risorse produttive), effettuando piccoli aggiustamenti sulla linea di produzione stessa durante le lavorazioni, analizzando e ottimizzando i ritardi sulla catena di montaggio, oppure per migliorare le variabili associate all’efficienza energetica. Inoltre, una migliore connettività e comunicazione tra la catena di montaggio e la produzione consente ai produttori di essere più vicini alla domanda del mercato e di personalizzare ciò che stanno costruendo, in base alle puntuali esigenze dei clienti, evitando sprechi e adeguando rapidamente i programmi di produzione ai cambiamenti della domanda o ad inaspettate interruzioni della catena di fornitura. I sensori possono essere utilizzati anche per monitorare e prevedere la qualità dei prodotti finiti, ad esempio, misurando costantemente la temperatura, le vibrazioni e l’umidità di produzione o adottando sistemi di visione a intelligenza artificiale per ispezionare ogni prodotto che esce dalla linea.
Cybersecurity & Privacy vs. IIoT
L’IIoT favorisce una migliore connessione e un maggiore flusso di dati, permettendo di attuare rapidamente, da remoto, le misure di cyber security in termini di aggiornamenti di software critici e del firmware dell’hardware. È risaputo che, nel contesto industriale delle smart factory e del modello IIoT, volto all’ottimizzazione dei costi e dei processi produttivi, le aziende sono chiamate a rispondere a importanti esigenze di sicurezza del patrimonio informativo, soprattutto quando si tratta di gestire i dati delle persone fisiche.
La sicurezza informatica è fondamentale, non solo per ovviare alla perdita di dati, ma anche per evitare i malfunzionamenti dei macchinari: di fatto un modello di data-driven industry è particolarmente sensibile ad attacchi cyber, la cui gravità sarà commisurata all’attività svolta (i.e. centrale elettrica, ospedale, ecc.). Ne deriva la necessità diffondere quanto più la cultura digitale all’interno dell’organizzazione e di dotare il personale delle skill necessarie per l’utilizzo adeguato della tecnologia implementata, oltre a adottare, per prevenire e mitigare i potenziali cyber attack, tutte le misure necessarie, quali:
- lo svolgimento di attività di Business Impact Analysis (BIA) e di Risk Assessment (RA), per identificare l’impatto dell’IIoT sull’organizzazione a livello operativo, finanziario, competitivo e reputazionale;
- l’identificazione dei punti di contatto dei sistemi basati sull’IIoT che interagiscono tra loro e con le persone;
- il censimento aggiornato delle relazioni tra le varie piattaforme tecnologiche, partendo dal presupposto che tutto sarà collegato a qualcosa, in modo tale da avere una visione a 360°;
- la puntuale gestione dei dispositivi IIoT in base alla loro tolleranza del rischio, determinando altresì un budget per la protezione delle risorse e dei dispositivi stessi;
- la protezione del perimetro della rete mediante: firewall (che devono essere sempre aggiornati), sistemi di rilevamento e di prevenzione delle intrusioni, impiego di tecnologie avanzate di monitoraggio della rete, software antivirus e antispam, azioni anti-phishing;
- la crittografia dei dati, sia inattivi che in transito;
- la replica dei sistemi critici, macchine virtuali e dati, in modo da poter ricreare l’ambiente originale.
È necessario ricordare che l’IIoT non comprende soltanto la gestione e l’elaborazione di informazioni inerenti alla mera scadenza della manutenzione di un macchinario o all’ottimizazione della produzione. Esso, infatti, include altresì la raccolta dei dati di soggetti che, a vario titolo, si trovano a interagire con la smart factory, i.e. dipendenti, fornitori, clienti, ecc. Pertanto, è necessaria l’adeguata gestione delle implicazioni derivanti dalla messa in essere dei principi e degli adempimenti richiesti dal quadro normativo in materia di protezione dei dati personali.
Tutti i sistemi e i macchinari connessi delle linee di produzione, in grado di raccogliere e trattare big data – che successivamente vengono condivisi in rete – dovranno necessariamente rispondere al principio di privacy by design contenuto nell’art. 25 GDPR. Le soluzioni a tutela della riservatezza dei dati personali, secondo questo principio, dovranno essere garantite fin dalla fase di progettazione del processo aziendale e per l’intero ciclo di vita di quest’ultimo, al fine di prevenire i rischi (c.d. risk based approach), non solo nel momento in cui il trattamento viene “pensato”, ma anche durante la fase di esecuzione del medesimo e fino all’ultimo utilizzo ed eliminazione del dato.
Sarà altrettanto fondamentale rispettare il cosiddetto principio di privacy by default, anch’esso contenuto all’interno dell’art. 25 GDPR, secondo cui per “impostazione predefinita” dovranno essere trattati solo i dati personali necessari al perseguimento delle finalità previste e per un periodo di tempo strettamente connesso a tale fine.
Si tratta di incorporare il concetto di privacy nell’intero percorso produttivo, attraverso la previsione di tecniche di anonimizzazione, pseudonimizzazione e minimizzazione dei dati, in modo che il trattamento degli stessi sia pertinente e non eccedente rispetto alle finalità (cfr. art. 5, comma 1, lett. c) GDPR) dato che un macchinario, pur non elaborando direttamente dati personali, potrebbe riceverli da un altro dispositivo ad esso connesso (caratteristica propria dell’IIoT, dove l’efficacia e la produttività aumenta quanto più i sistemi sono connessi e dialogano gli uni con gli altri).
La vera sfida del processo di digitalizzazione industriale si traduce, pertanto, nella capacità dell’impresa di sfruttare al massimo i benefici dell’IIoT individuando soluzioni che siano in grado di facilitare il conseguimento degli obiettivi fissati, ma nel pieno rispetto della normativa in materia di privacy.
Conclusioni
Nella ripresa delle attività le imprese devono dimostrarsi sempre più agili e flessibili per far fronte ai repentini cambiamenti del mercato di riferimento, dal momento che diventa cruciale saper indirizzare sfide e rischi che richiedono una risposta subitanea in termini di: gestione della forza lavoro, flessibilità della supply chain, andamento discontinuo delle vendite, ordini ai fornitori e limitazioni negli spostamenti che penalizzano la circolazione delle merci.
L’impiego dell’IIoT può contribuire a raggiugere la resilienza necessaria per poter rispondere prontamente alle sollecitazioni contingenti; tuttavia, implica l’acquisizione della cultura digitale da parte di tutta l’organizzazione, oltre a un profondo cambio di paradigma. Le aziende devono fare un’autoanalisi e, grazie al supporto di professionisti qualificati, implementare principi di Risk Management e Business Continuity che, mediante un approccio olistico, contribuiranno a garantire: la condivisione dei piani di rischio, dei piani di continuità aziendale e dei piani di crisi; la comunicazione puntuale di ciò che ogni piano comporta e come si evolverà, cercando allo stesso tempo il coinvolgimento e il contributo di tutti gli attori (interni ed esterni all’organizzazione) coinvolti.
L’approccio reattivo al cambiamento ha ripercussioni nel breve periodo nella gestione dei rischi attivi che si sono già verificati e concretizzati, mentre l’approccio proattivo si evidenzia nel medio-lungo termine, identificando e mitigando i rischi potenziali prima che si concretizzano. La storia ci insegna che, nei momenti di crisi, le aziende che meglio si strutturano al cambiamento, dimostrando adattabilità e flessibilità, saranno quelle in grado di recuperare quote di mercato e di emergere in modo dirompente.
Articolo a cura di Federica Maria Rita Livelli
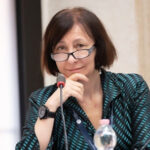
Certificata in Risk Management (FERMA/ANZIIF certificazioni Iso 3100:2018) & Business Continuity (AMBCI Certification – BCI, UK; CBCP Certification – DRI, Usa), svolge consulenze in Risk Management & Business Continuity oltre ad effettuare un’attività di diffusione e sviluppo della cultura della resilienza presso varie istituzioni e università italiane e straniere. Ricopre anche il ruolo di Training Director presso BeDisruptive Consulting.
Membro de:
· ANRA (Associazione Nazionali Risk Manager & Responsabili Assicurazioni Aziendali) – Membro Comitato Direttivo
· BCI, UK (Associazione Internazionale Business Continuity & Resilience) – Membro del Conduct Committee
· BCI CYBER RESILIENCE SIG – Board Member
· CLUSIT (Associazione Italiana per la Sicurezza Informatica) - Membro Comitato Scientifico e Gruppo CLUSIT AIXIA
· ENIA (- Ente Nazionale per l’Intelligenza Artificiale) - Membro Comitato Scientifico
· FERMA (Federation of European Risk Management Associations) – Membro of Digital Committee
· UNI (Ente Nazionale Italiano di Normazione) - Rappresentante per ANRA al Comitato Tecnico UNI/CT 016/GL 89 "Gestione dell'innovazione" (ISO/TC 279) (Commissione Tecnica -UNI/CT 016 "Gestione per la qualità e metodi statistici")
Speaker in numerosi seminari e convegni nazionali ed internazionali in riferimento a tematiche di Business Continuity & Risk Management, Resilience , Change Management, Innovazione, Cyber Security, Facility Management & Procurement e Artificial Intelligence
È altresì autrice di numerosi articoli inerenti alle tematiche di Risk Management & Business Continuity, Cybersecurity e Resilience pubblicati da diverse riviste italiane e straniere. Co-autrice de: Report 2020-2021-2022 -2023-2024 CLUSIT-Cyber Security e de “Lo stato in Crisi” ed. Franco Angeli.